Rolling Up Item Costs
You will see the window shown below. If only rolling up the cost of the selected item click the Item Only button. If you wish to roll up all items in the system click on the All Items button. This may take a bit of time as the system rolls up the cost of each item in the database.
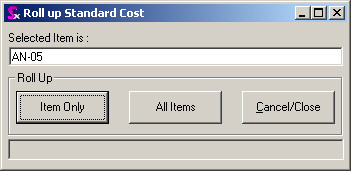
Item Main Assembly Setting
By default when you tag an item as Make, the Assembly checkbox will be automatically checked. As a step further, when both the Make and Buy flags are activated (with default of Assembly), the roll up of the item will include the entire child item and labour costs associated with the parent. (An Item must be flagged as Assembly to roll up any costs and weights from the child items).
For situations where the item is tagged both Make and Buy and you want to roll up the vendor costs instead of the child item costs, switch the Assembly flag off. If the user overrides the default setting and switches the Assembly flag off, the Vendor’s cost will be converted to home currency and multiplied by Freight, Duty and Overhead Factors to calculate the replacement cost. The replacement cost will be used in the roll up calculations. The roll up will ignore the child item and labor costs as well as child item weights. The user must manually enter the weight.
Costing Options
OrderStream offers very flexible and powerful costing options. This includes Standard Costing, Most Recent Costing, Replacement Costing and Actual Costing.
Activity Based Costing (ABC)
An accounting technique that allows an organization to determine the actual cost associated with each product and service produced by the organization. ABC is an alternative to the traditional way of accounting. ABC is a costing model that identifies the cost pools, or activity centers, in an organization and assigns costs to products and services (cost drivers) based on the number of events or transactions involved in the process of providing a product or service. ABC will help identify the most and least profitable customers, products and channels. It will also assist you to determine the true contributors and detractors from financial performance. Seradex supports Activity Based Costing. This should be discussed with your Project manager.
Standard Cost
The expected labor and material cost for an item for a specified fiscal period against which variances are measured and evaluated. Standard costs provide management with goals to attain as well as a basis for comparison with actual results. Variances can be tracked on material price or quantity, labor time or hourly rates, scrap and exchange rate fluctuations. This is a management tool that requires discussion with your controller and possibly outside accountants. Some organizations will freeze the standard cost for 3 or 12 months.
Most Recent Cost
The cost based on the last prices paid for all the buy items used in this item if it is a make item or the last price paid to the vendor if a buy item. The prices are converted to home currency at the current exchange rate as multiplied by the freight, duty and overhead factors assigned to the buy items. If you have not purchased the item for an extended period of time it may not be an accurate replacement cost.
Replacement Cost
The cost based on the current vendor prices you would have to pay if you purchased the item today. The prices are converted to home currency at the current exchange rate as multiplied by the freight, duty and overhead factors assigned to the buy items.
Actual Cost
For a buy item this is the actual cost paid for the item on the PO converted to home currency. For a make item it is the sum of the actual costs of all the buy items used in production plus the actual labor hours x the cost per hour of the work center from data collection records. Some companies prefer to use the actual material costs and the standard labor costs. There are many costing configurations available
Costing Examples
Item IPTQUARTCAN has a Standard Cost, Most Recent Cost, Replacement Cost and an Actual Cost of $1.00 CAN.
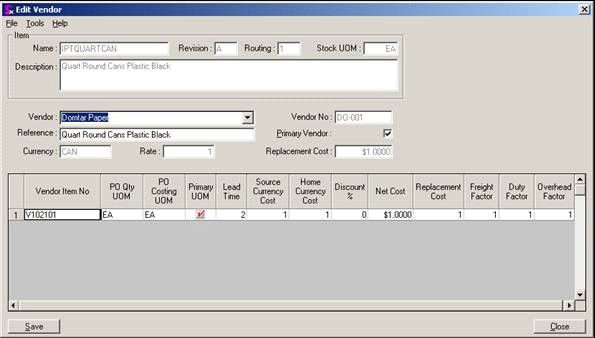
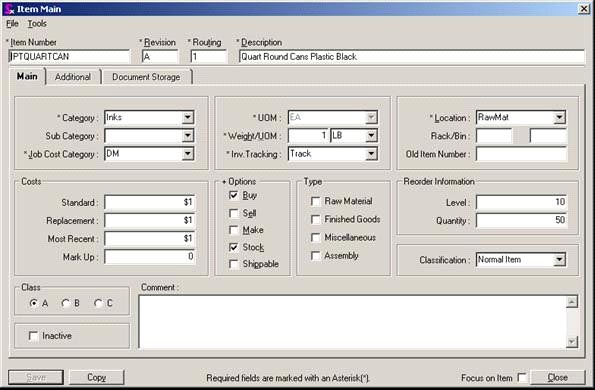
Case A: Price Increase
The following chart explains how standard costs are managed in OrderStream.
|
|
|
|
|
|
1
|
Issue a purchase order for item A where the cost has changed to 1.20 C$ from 1.00 C$ per item.
|
1.00
|
1.00
|
1.00
|
1.20
|
2
|
Receive the purchase order for item A
|
1.00
|
1.20
|
1.00
|
1.20
|
3
|
Change the Vendors Source Cost in the Item Editor and perform an item roll up.
|
1.20
|
1.20
|
1.20
|
----
|
4
|
Issue a purchase order for item A, and the cost has changed to 1.22. The user manually changes the cost on the PO from $1.20 to $1.22
|
1.20
|
1.20
|
1.20
|
1.22
|
5
|
Receive the purchase order for item A
|
1.20
|
1.22
|
1.20
|
1.22
|
Case B: Price Increase and Multi Currency
Item “A” had a standard Cost, a Most Recent Cost, a Replacement and an Actual Cost of 1 U.S. dollar and an exchange rate of 1.3444. The following chart explains how standard costs are managed in OrderStream with an exchange rate.
|
|
|
|
|
|
|
1
|
Issue a purchase order for item A at a cost of 1.00 U.S. dollar per item.
|
1.3444
|
1.3444
|
1.3444
|
1.3444
|
1.3444
|
2
|
Receive the purchase order for item A
|
1.3444
|
1.3444
|
1.3444
|
1.3444
|
1.3444
|
3
|
Change the Vendors Source Cost to 1.20 U.S. dollars in the Item Editor and perform an item roll up.
|
1.3444
|
1.6133
|
1.3444
|
1.6133
|
----
|
4
|
Exchange rate changes to 1.50 and an item cost rollup is performed
|
1.5000
|
1.8000
|
1.3444
|
1.8000
|
----
|
5
|
Issue and receive a PO for 1.20 U.S.
|
1.5000
|
1.8000
|
1.8000
|
1.8000
|
1.8000
|
The Most Recent Cost is only update in the case where you buy the item.
Note: The above charts are premised on having the Application Preferences standard cost rollup check box selected.
Case C: Tracked Buy Sell Item
|
|
|
|
|
|
|
|
0
|
0
|
0
|
0
|
0
|
2.45
|
Off
|
|
Perform a root item roll up and click yes at this message:
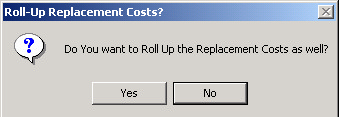
|
2.45
|
2.45
|
0
|
0
|
0
|
2.45
|
Off
|
|
Change the vendor Freight, Duty and Overhead Factors
|
2.45
|
2.45
|
0
|
0
|
0
|
2.45
|
Off
|
|
Perform a root item roll up and click yes at this message:
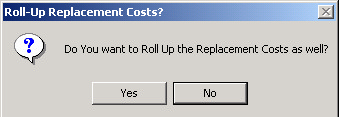
|
2.6034
|
2.6034
|
0
|
0
|
0
|
2.45
|
Off
|
|
Issue Purchase Order for above item - Receive into inventory by approving the Receipt.
|
2.6034
|
2.6034
|
2.45
|
0
|
0
|
2.45
|
Off
|
|
Perform a root item roll up and click yes at this message:
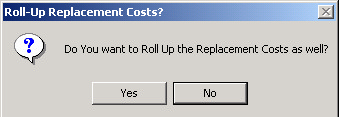
|
2.6034
|
2.6034
|
2.45
|
0
|
0
|
2.45
|
Off
|
|
If No is selected on the Roll-Up Replacement Cost? Message box the results:
|
0
|
0
|
2.45
|
0
|
0
|
2.45
|
Off
|
|
Case D: Tracked Make/Sell Root Item With BOM
Working with the following item set-up: 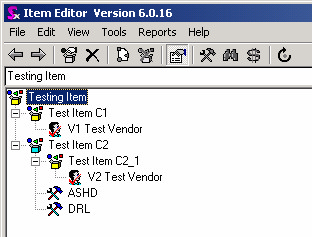
|
Testing Item: Make/Sell
Standard/Replacement/Most Recent Cost: $0
|
Test Item C1: Buy/Stock
Standard/Replacement/Most Recent Cost: $0
Reorder Level = 1 Reorder Qty = 1
|
V1 Test Vendor: Source Cost $3.2500
Factors: Freight = 1 Duty = 1 Overhead = 1
|
Test ItemC2: Make/Stock
Standard/Replacement/Most Recent Cost: $0
|
Test ItemC2_1: Buy/Stock
Standard/Replacement/Most Recent Cost: $0
|
V2 Test Vendor: Source Cost $4.2500
Factors: Freight = 1.02 Duty = 1.05 Overhead = 1.002
|
ASHD: Assembly Work Cell
Labour. Rate $20/hr
Set up/Run Time: 2 min/3 min
Total Cost = $1.00*
|
DRL: Drilling Work Cell
Labour Rate $20/hr
Set up/Run Time: 2 min/1 min
Total Cost = $0.3333**
|
Testing Item Output:
|
|
|
|
|
|
|
|
0
|
0
|
0
|
0
|
0
|
N/A
|
Off
|
Perform a root item roll up and click yes at this message: 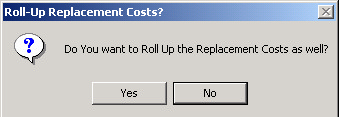
|
$9.1442
|
$0
|
$0
|
0
|
0
|
N/A
|
Off
|
* ASHD: Since the “Include Labour Setup Time In Cost” flag is off labour cost is 3 min x $20 per hour = $1.00
** DRL: Since the “Include Labour Setup Time In Cost” flag is off labour cost is 1 min x $20 per hour = $0.3333
|
Testing Item Output:*
|
|
|
|
|
|
|
|
$10.4775
|
$0
|
$0
|
0
|
0
|
N/A
|
Off
|
*“Include Labour Setup Time In Cost” flag is On labour costs are:
ASHD: (2 min setup+= 3 min run) x $20 per hour = $1.6667
DRL: (2 min setup + 1 min) x $20 per hour = $1.0000
|
|