Items
Sub Contract Parents
The recommended setup for a Sub Contract Parent is non Buy and non Make. A Sub Contract Parent is not setup as buy because it does not have a direct Vendor. It is not setup as Make because the Sub Contract Parent is not manufactured by the company using the part. The Sub Contract Service and Materials have Vendors associated to them.
Sub Contract Services
The recommended setup for Sub Contract Services is buy and non stock. The inventory tracking type should be set to No Tracking. Service items do not physically exist and should not be entered into inventory.
Sample
The Sub Contract module was developed to assist manufacturing companies dealing with sub contractors. The basic scenario is that a company sends material to a vendor to be processed in an operation like machining or painting. This business process involves material requisitions, purchase orders, inventory transfers, receipts and vendor invoicing.
To illustrate the functionality we will use an example transaction from our sample database. The bill of material in the example illustrates the set up for an item; _ChairItem. The _ChairItem is manufactured by sending _Tube to a vendor (Green Metal Cleaning) for painting. The _Tube is purchased from Atlas Stainless Steel.
After the _Tube is painted, it is designated as a new item number _CF (Chair Frame). The Chair Frame can then be assembled with other components to make the _ChairItem.
Note: Vendor Locations for all Sub Contract Service Vendors MUST be identical tousing the Vendor’s AP Vendor Code.

|
|
|
|
|
|
|
|
|
_ChairItem
|
Chair
|
Make
|
Tracked
|
Normal
|
Yes
|
50
|
100
|
EACH
|
_CF
|
Chair Frame
|
N/A*
|
Tracked
|
Sub Contracted Parent
|
No
|
N/A
|
N/A
|
FT
|
_Tube
|
Tube
|
Buy
|
Tracked
|
Normal
|
Yes
|
500
|
100
|
FT
|
_Paint
|
Paint
|
Buy
|
No Tracking
|
Sub Contracted Service
|
No
|
N/A
|
N/A
|
EACH
|
The Sub Contract Parent designates the completed item after the sub contract is finished. The Sub Contract Service designates a sub contract operation.
Vendor Locations
Inventory locations must be setup for each Sub Contract Service vendor. The Location Code must be the Vendor Number of the vendor providing the service.
To setup a new Location, go to Lookups and select Locations to open the following form:
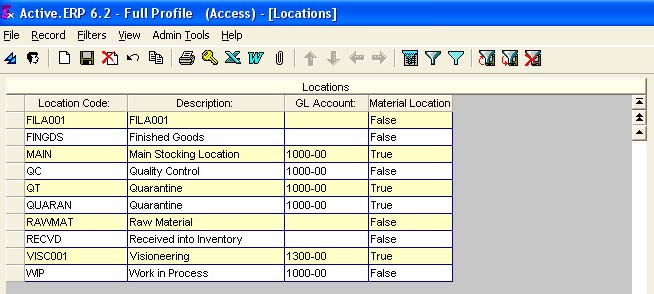
Go to Record and select Add. The following window will be displayed:
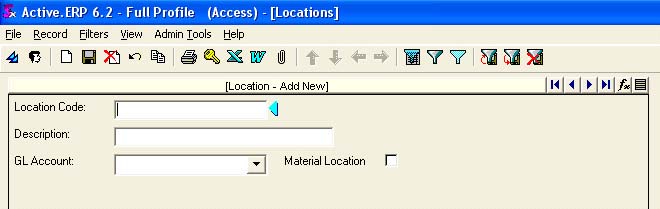
In the Location Code field enter the vendor number of vendor providing the service.
The Description can be anything, for example, the name of the vendor.
Optional: To set the GL Account, click the drop down arrow to display a list of GL Accounts currently in the system and select the correct account. If you do not want to specify a GL Account the field can be left blank.
Now that the Location is setup, go to the Item Editor and open the Item Master of a Sub Contract Service item that is purchased from the Vendor Location that was just created. Set the item Location to the Vendor Location. Should an alternate vendor be required change the Location (new Vendor code) on the Mat Req detail line.
Application Preferences
Auto Generate Sub Contract Document from Sales Order/Work Order
When this option is checked in application preferences Sub Contract documents are created automatically via Mat Req.
Please note that Inventory Levels of the Sub Contract parent are not checked.
To generate the Sub Contract document from a Sales Order or Work Order go to Tools, Generate Material Requisition.
Note: If the Subcontract parent is set to Stock and the Reorder Qty is greater than 0 then the logic will not generate a Subcontract order but rather will be incorporated in the MRP and Reorder Items logic.
When the Mat Req generation is complete, you will be able to view the Sub Contract document in the Sub Contracting module where you will be able to manually Evaporate or Transfer necessary raw materials and generate the Mat Req for the correct amount of the required service.
Auto Generate Sub Contract Material Requirements from Sales Order/Work Order
When this option is selected in application preferences the material requirements for Sub Contract parents are created in Mat Req. This option is designed to be used in tandem with Auto Generate Sub Contract Document from Sales Order/Work Order.
Using this option will yield the following results: A Sub Contract document will be created and the total required amount of the attached service will be allocated. A Mat Req for the service will be generated automatically. Please note that the Raw Material will not be allocated for either Evaporation or Transfer. This step must be performed manually.
To generate the Sub Contract material requirements from a Sales Order or Work Order go to Tools, Generate Material Requisition. If the material items are Buy and Stock and the Reorder Level is greater than 0 then they are incorporated in the Reorder Items and MRP logic.
When the Mat Req generation is complete, open the Mat Req module and enter the appropriate Sales Order/Work Order number. To view only Sub Contract children, use the Item Type filter to display Sub Contract-Child. The Sub Contract Parent that the displayed Child belongs to is indicated in the comments field on the Mat Req form. You will notice a new column containing the related Sub Contract number will be inserted when you use the Sub Contract-Child filter. Double click the Sub Contract number to open the Sub Contract document as seen in the example below.
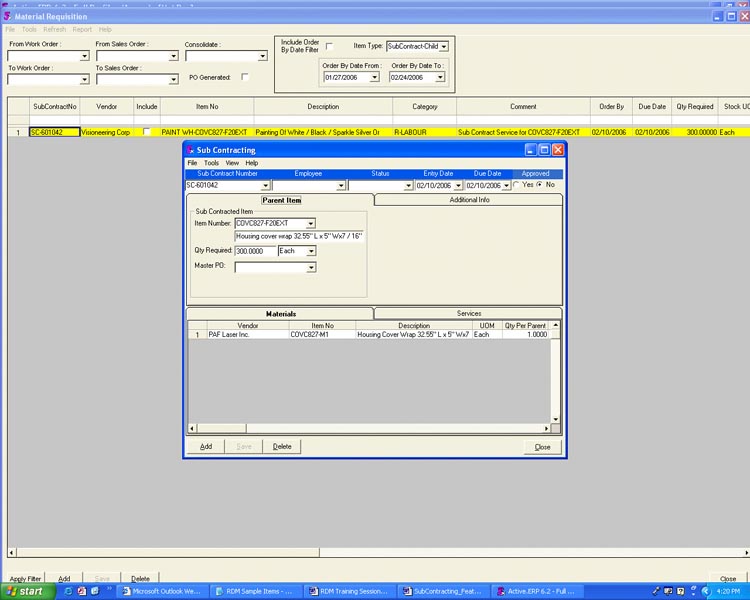
For sub contract parent items that contain non stock make children as part of their bill of material, this preference will also automatically generate work orders for the required make children.
Auto Completion of Sub Contracting Documents from Receipt Approval
When this option is checked in application preferences, the Sub Contracting completion window will appear after you approve a receipt of the Service purchase order.
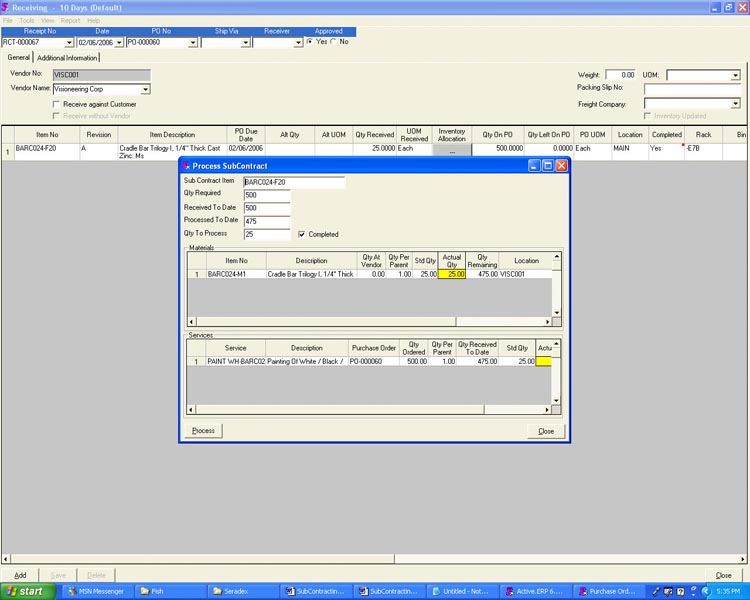
The qty to process field is populated with the quantity of the current receipt.
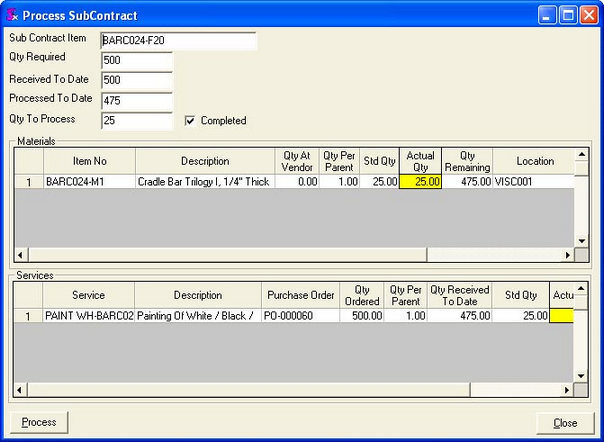
Past receipts and processing are tracked and totalled in the Received To Date and Processed To Date fields respectively.
Click the Process button to process the Sub Contract document. The following prompt will appear when processing has completed.
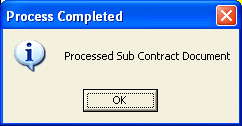
Close the Sub Contract processing window to return to the Receiving Module.
|