Receiving Sub Contract Parents Manually
The following process applies if the Auto Complete Sub Contracting Document from the Receiving Update Inventory menu application preference is not enabled.
Go to Receiving and receive the Green Metal Purchase Order as shown below:
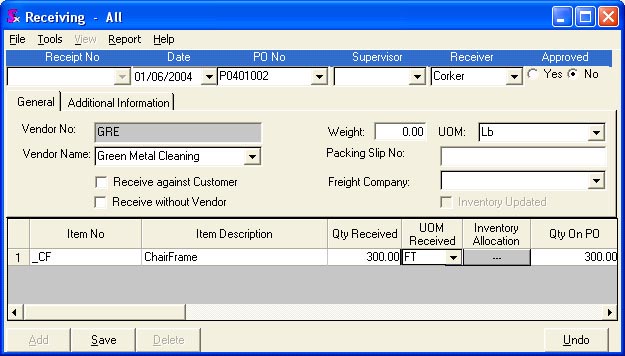
You will note that the item received is automatically set to _CF even though the original PO to Green Metal was for painting. The system does this automatically and is based on the bill of material setup using the sub-contracted designations as outlined at the start of the section.
After completing the receipt there is 300 EACH of the _CF on hand:
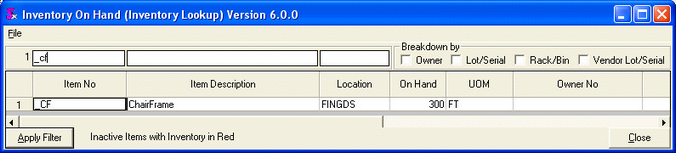
To complete the Transaction open the Sub Contract form and select the correct Transaction number.
Under Tools select the Complete menu option.
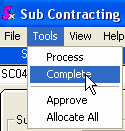
The following form is displayed:
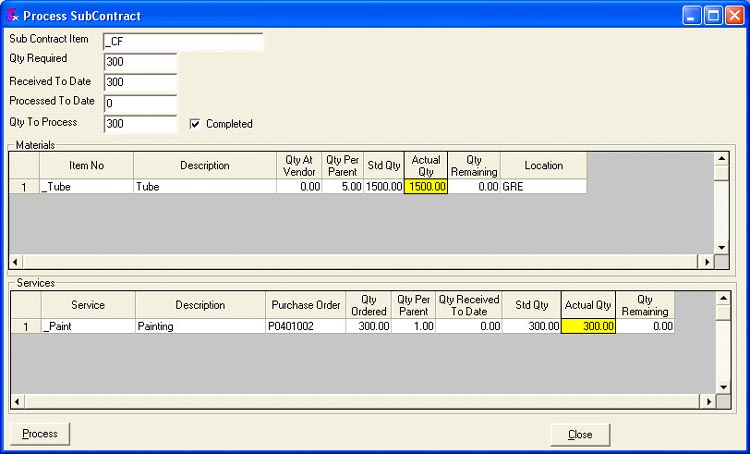
You can manually edit the Quantities shown in yellow. For example if your supplier scrapped some tubing you could change the amounts.
After the processing is completed, the _Tube is deducted from the Vendor Inventory and the system is set up to process an invoice from Green Metal for 300 units of painting.
Receiving Nested Sub Contract Parents Generated via Transaction Lookup
Nested sub contract parents must be received and processed before the top level sub contract parent can be received. When the nested sub contract parent is received, the received inventory will be inserted into the vendor location designated for the service belonging to the sub contract parent one level above the nested sub contract parent.
For example, V1116 is the vendor location designated to the service for the top level sub contract parent and E3337 is the vendor location designated to the service for the nested sub contract parent. When the nested sub contract parent is received, the amount received is inserted into V1116 since the material is being shipped from one vendor to the next. When the top level sub contract parent is received, the inventory in V1116 will be evaporated and inventory for the top level parent will be added into the top level parent’s default inventory location.
Notes:
The amount of the nested sub contract parent that will be evaporated is equal to the amount required by the qty of the top level sub contract parent received. If you used the main MRP form to generate your sub contract documents you will have to manually create an inventory transfer to insert the nested sub contract parent into the top level parent’s inventory location.
Using the Transaction Lookup will transfer the exact material quantity required by the related parent document in the vendor location automatically.
If buy stock materials are required to be purchased to satisfy sub contract documents, using the Transaction Lookup will automatically set the ship to address of the purchase order to that of the applicable service vendor and the receiving location to that of the service vendor location. If the Transaction Lookup is not used (the main MRP form is used), the ship to will be your plant and the receiving location will be the default inventory location for the buy stock item.
Sub Contract Parent Most Recent Cost Roll Up
The Most Recent Cost of the Subcontract Parent is determined by taking the Most Recent Cost of the raw materials and adding it to the Most Recent Cost of the service. The update occurs at the time the Sub Contract Parent is processed after receipt.
Impact on Accounting
The processing of sub contract documents does not have an impact when posting GL transactions during Day End Processing. The total cost of a sub contract parent is posted to your accounting system in two phases: 1) the receipt of the child materials(s) and 2) the receipt of the service item. The total consolidated cost of the sub contract parent is NOT posted by Day End Processing after a sub contract service purchase order has been received and the related sub contract document has been processed.
An Important Note Regarding Sub Contract Material Transfers:
OrderStream has the ability to post inter location inventory transfers during Day End Processing. This feature is enabled via the Use Location GL Account for Inventory application preference. With this preference enabled, if there is an inventory GL account assigned to the locations specified on the transfer, the inventory cost of the items being transfered will be included in the Day End Processing batch when posting GL Inventory Transfers.
If you have User Location GL Account for Inventory application preference enabled it is important that you do not have an inventory GL account specified against the sub contract locations set up in OrderStream. Failure to comply with this warning may cause unbalanced GL entries.
|