To view the demand on an item at a transaction level, double click the appropriate line item in the transaction column you wish to view. For example, to view demand on an item from Estimates, double click the line containing the item in question in the Qty Req Est cell. The window below will then open.

Each estimate for which there is insufficient inventory for the item in question will be displayed.
Adding Items to Mat Req
Note: These steps can only be completed for Sales Order, Work Order and Sub Contracting transactions. Material cannot be sent to the Mat Req from Estimate transactions.
On the line containing the item you wish to purchase, you can double click the Qty Req SO, the Qty Req WO, or the Qty on Sub Con fields. For the purpose of this example, we will look at the Qty Req SO.
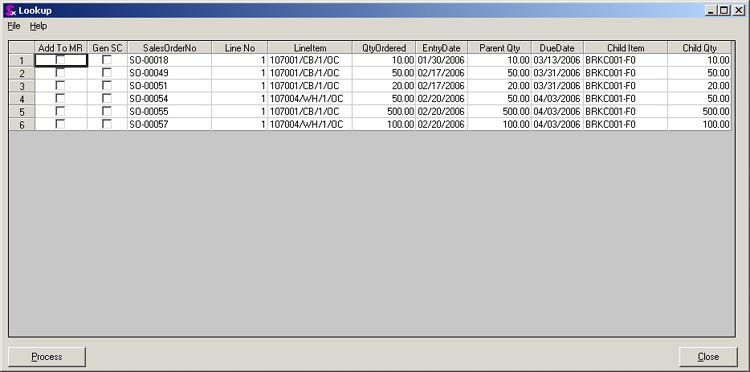
The columns represent the same data as stated for the estimate lookup, but two new columns are featured.
1. | Add To MR (Normal Stock Items) |
To add the child item quantity required by each sales order directly to the Mat Req, check the Add To MR box for all applicable sales orders and click the process button.
You will see the selected items being added to the Mat Req form in the background. Unselected items will remain until the decision is made to proceed with purchasing for these orders.
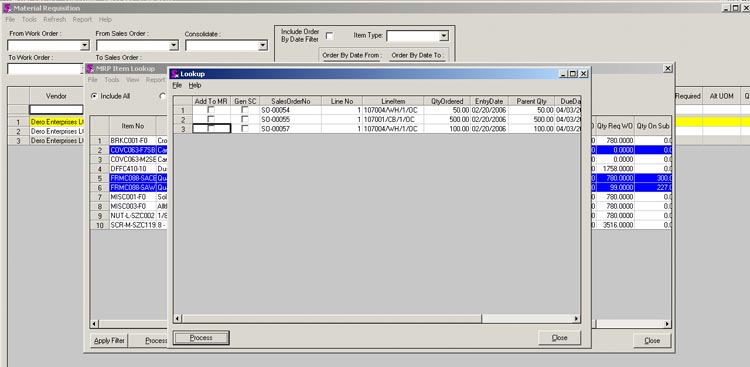
When you close the lookup window, the MRP form will reload and update the Qty Req SO quantity. The quantity of the item sent to the Mat Req will be subtracted from the Qty Req SO.
2. | Gen SC (Sub Contract Parents) |
If the reorder item is a sub contract parent the Lookup window will look as it does below:
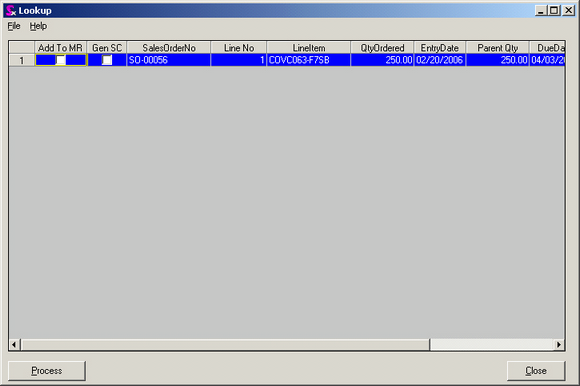
To directly generate a sub contract document, check the Gen SC box then click the Process button. You will be prompted with the newly created sub contract number.
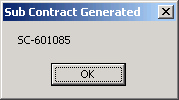
When you close the lookup window, the MRP Form will reload and update the Qty Req SO.
Note: You may also add sub contract parents to the Mat Req and generate the sub contract document from there.
Viewing Reorder Information
The reorder level and quantity of a child item can be viewed in the Transaction Lookup Form. To view this information, the user must simply place their cursor over the child item number. The reorder information will be displayed as a tooltip as shown below.

Assigning Owner Information
By default, adding stock items to the Mat Req or generating subcontract documents via the Transaction Lookup form will assign ownership information (the source sales order or work order) to the items being purchased for reference purposes only. When a purchase order generated in this method is received, the item(s) will not be allocated to the source work order or sales order. If this functionality is not desired, it may be disabled by checking the Disable Assigning Owner Info from Buy/Stock MRP Lookup option on the General tab in Application Preferences.
After items have been added to the Mat Req via the Transaction Lookup form and the form has been closed, the main MRP form will reload. Once the reload is complete, the quantity required by the relevant transaction type will be reduced by the quantity sent to the Mat Req. The total quantity required by all transactions will be reduced by the same amount (if the Disable Assigning Owner Info from Buy/Stock MRP Lookup application preference is NOT enabled). For example, if you have a total of 500 CLT-1003 required by open work orders and you send 100 to the Mat Req via the Work Order Transaction Lookup form, the new quantity required by open work orders as displayed on the main MRP form will be 400. Note that if the Disable Assigning Owner Info from Buy/Stock MRP Lookup application preference is enabled, the system will not be able to track the quantities that have added to the Mat Req from the Transaction Lookup Form.
Modifying Quantity to Order
It is possible to change the quantity to send to the Mat Req on the Transaction Lookup form by modifying the value in the Child Qty field.
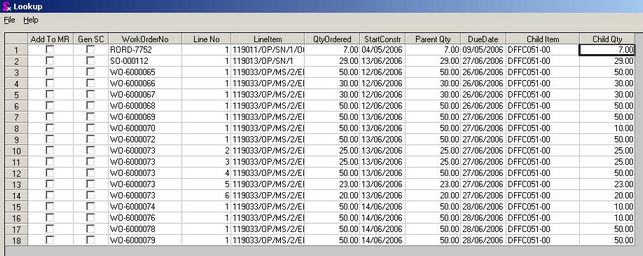
Modifying this field will override the original quantity to buy and the updated value will be sent to the Mat Req. Once the Transaction Lookup form is closed and the main MRP form reloads, the required quantities will be recalculated using the updated value.
There are some factors to be aware of when modifying the Child Quantity field. Referring to the above screen shot, if the Child Qty of line 1 was changed to 36 to consolidate lines one and two (7 + 29), line two will still be displayed the next time MRP is run and the Transaction Lookup is opened.
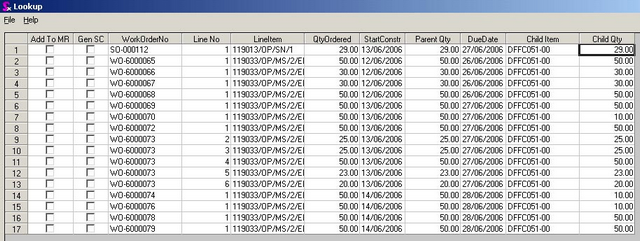
The reason this occurs is due to the fact that unless a Transaction Lookup line has been sent to Mat Req by checking the Add To MR button and clicking Process, the system has no way of knowing that the line should no longer appear in the Lookup. Thus, changing the Child Quantity on the Transaction can cause the total quantity required displayed on the Transaction Lookup to be different from the total quantity displayed on the main MRP form.
Field Reference
|
|
Transaction No
|
The transaction number. To view the actual estimate double click estimate number you wish to view.
|
LineNo
|
The line number on the estimate of the parent item containing the reorder item.
|
LineItem
|
The item number of the parent item containing the reorder item.
|
Parent Qty
|
The quantity of the parent item on the estimate.
|
Due Date
|
The due date of the estimate.
|
Child Item
|
The name of the reorder item from the MRP Form
|
Child Quantity
|
The quantity of the reorder item required to satisfy the estimate.
|
|